A diferencia de los centro de producción de Michelin, en el Centro de Experiencias de Michelin de Almería —CEMA de aquí en adelante— no se fabrican neumáticos, sino que se destrozan, se diseccionan, se analizan… se hace una verdadera labor de cirujano y forense. En realidad, se buscan sus límites y posibles debilidades llevando las condiciones de pruebas a los extremos para la función específica que va a acometer ese neumático en concreto.
Michelin, comprometida con el medio ambiente
Es el principio del fin. Si algo no funciona adecuadamente se corrige y se vuelve a prototipar otro neumático con las especificaciones mejoradas hasta que desde el CEMA se verifica que se ha cerrado el círculo. Su especialidad es la obra civil, grandes neumáticos para minería, también aviación y neumáticos para turismo, especialmente en lo que concierne a pruebas de ruido o resistencia de rodadura, aunque unos y otros tienen nuevos retos y compromisos.
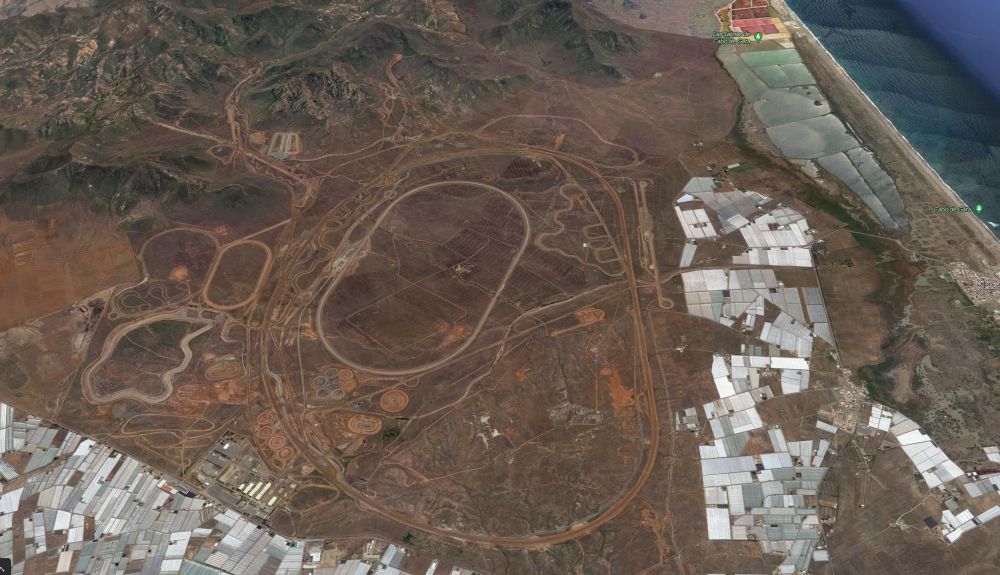
Y es que, la sostenibilidad es clave en Michelin desde hace décadas, cumpliendo su libro de ruta al dedillo para ofrecer neumáticos con la mejor calidad pero también respetuosos con el medio ambiente. 2050 es la fecha establecida por la marca para que todos los neumáticos que produce la marca sean 100% sostenibles y estén fabricados por materiales reciclados o de origen biológico y ya en 2030 nos asegura Michelin estar capacitada para alcanzar un 40% de componentes sostenibles en sus ruedas. 6.000 expertos en todo el mundo y más de 698 millones de euros en inversiones anuales destinadas a investigación y desarrollo se encargar de lograr el producto más “redondo”, 170 de los cuales lo hacen desde el CEMA, la joya de la corona de Michelin.
Visitar el CEMA nos ha permitido descubrir una nueva dimensión del neumático
Ubicado en pleno Parque Natural del Cabo de Gata-Nijar, visitar el CEMA te cambia por completo la perspectiva que tienes de un neumático, las exigencias que impone la marca y los límites extremos en los que se realizan los ensayos. Allí no se analiza la velocidad de paso por curva de un deportivo —que es también es viable—, sino la resistencia de una rueda de Dumper que carga 400 toneladas sobre una base de pórfido, una piedra con la que podrías sobrevivir en la selva por sus aristas cortantes, sometido a 600 minutos de ensayo y cambiando la superficie cada 30 minutos. O la rotación de un neumático sobre la llanta de una excavadora al encarar un montículo de tierra durante horas y horas de continuo trabajo. Dinero y eficiencia. Trasládalo al entorno de la minería, la obra civil o el transporte pesado y entenderás la importancia del concepto perfección.
Comprometido con el medio ambiente —Fue Declarado Parque Natural en 1987—, el CEMA es un laboratorio de pruebas inmenso que alberga pistas de tierra, de asfalto, talleres… Pero también talento y motivación de un equipo humano altamente cualificado liderado desde hace más o menos un año por Jorge Pato Elgoibar. Alrededor de 4.500 hectáreas albergan más de cien pistas en las que 250 vehículos recorren al año alrededor de 20 millones de kilómetros al año.
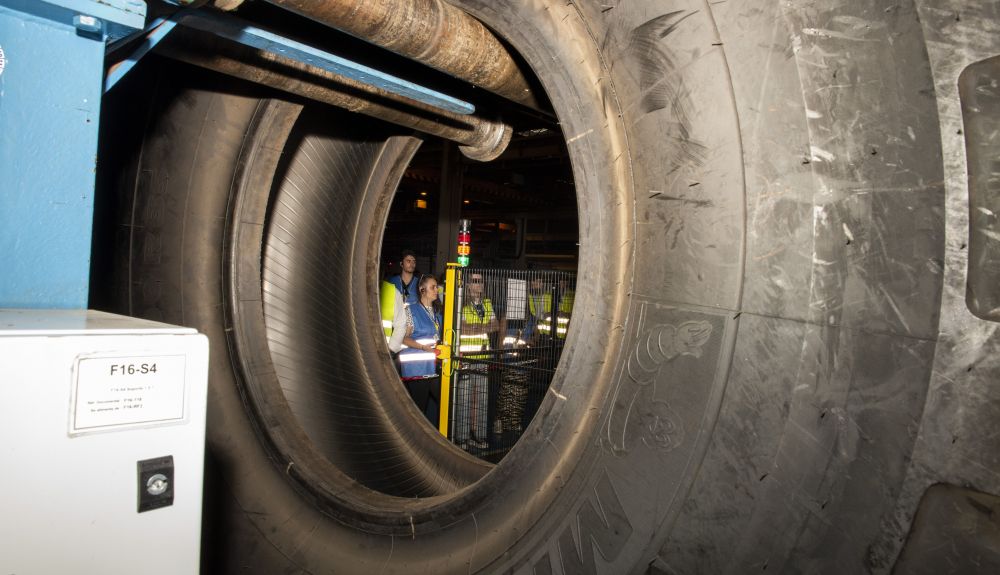
El CEMA te da una perspectiva completamente diferente del neumático porque no sólo sus pistas o instalaciones son hiperbólicas, sino que todo allí es gigante: sus vehículos de prueba, sus máquinas de rodaje autónomo, sus talleres de desmontaje y análisis donde se disemina el neumático con la intención de encontrar cualquier debilidad en su diseño y construcción. No en vano, allí se pone a prueba el neumático más grande del mundo, diseñado para el Caterpillar 979F, con un precio de 150.000 euros por rueda, 4 metros de diámetro, 63 pulgadas y 5,6 toneladas de peso. Un segundo Dumper de Caterpillar, el 798, completa la flota de vehículos de tamaño XXL que Michelin tiene en constante movimiento, a la que se suman otros vehículos destinados a obras, camiones de diferente tonelaje, tractores, camionetas y turismos “camaleónicos” que permiten definir un amplio espectro de huellas válido para otros vehículos de características concretas.
En el CEMA no se fabrica, se prueban características concretas definiendo test específicos
Cada tipo de neumático, por tanto, requiere un análisis específico definido por el fabricante ya que no se analiza sistemáticamente una característica concreta, y ahí es donde el CEMA ofrece sus servicios técnicos específicos estableciendo la metodología adecuada según las condiciones y seguimiento de cada prueba. Cada pista, por tanto, es dinámica, se modifica su trazado o estructura según el test a realizar y la característica que se pretenda medir. En la actualidad, totaliza cien kilómetros en constante crecimiento, pero siempre respetando el entorno, la flora y la fauna del parque.
Con sólo 3,5 kilómetros de prueba y 59 empleados el CEMA se convirtió desde el 2 de enero de 1973 en una pieza clave en el liderazgo de Michelin. Hoy, sigue siendo una herramienta colosal al servicio del desarrollo de los neumáticos de este fabricante. Es uno de los 9 centros que tiene la marca en todo el mundo y el más importante de Europa. Y no está en Almería por casualidad, sino por cumplir un exigente pliego de condiciones, especialmente en lo que concierne a estabilidad de temperaturas, estructura del terreno o baja pluviosidad, amén de otros aspectos puramente logísticos, unas condiciones ideales que no han hecho más que consolidad al CEMA como centro neurálgico de pruebas para neumáticos que darán servicio en cualquier rincón del mundo.
Y en sus 50 años, el CEMA no ha parado de sumar hitos. En 1977, por ejemplo, se puso en marcha la primera pista capaz de realizar pruebas de forma autónoma definiendo parámetros concretos —pista circular que emula técnicamente las condiciones de una recta infinita o bucles donde se prueba tracción, desgaste, durabilidad sobre diferentes configuraciones de terreno—. No es hasta mediados de los años 80 del pasado siglo cuando el CEMA asume también pruebas de neumáticos turismo, camioneta o avión para poco después, en 1982, poder ya realizar los primeros análisis no destructivos mediante rayos X y ultrasonidos.
Al final de esa década, en 1989, el CEMA inicia una nueva era en la automatización de los ensayos con máquinas de rodaje de desarrollo propio instaladas en los propios talleres, complementando así a las pruebas de exterior sobre terreno real. En 2015, se complementan las instalaciones con el primer brazo robótico junto a un microscopio, a lo que se suma una nueva máquina rodadora S14 a partir de 2020 junto a nuevos métodos de ensayo.
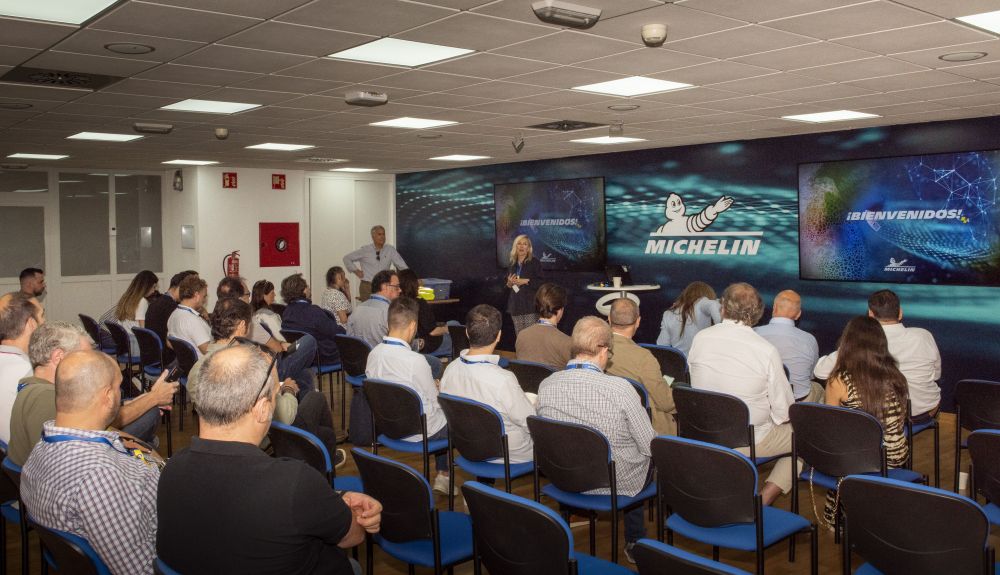
Como hemos dicho, se busca el talón de Aquiles del neumático, como puedes imaginar, en una dimensión desorbitada debido a las dimensiones de la gran mayoría de ruedas que se someten a prueba en ensayos que emulan en días de trabajo, el desgaste real de meses. La temperatura de trabajo es clave para poder optimizar su rendimiento, desgaste, resistencia de la estructura vital del neumático y poder por tanto modificar ciertos parámetros del neumáticos sus compuestos o estructura.
Para ello, ciertos neumáticos pasan a la “sala de cirujano” donde se monitorizan con termopares internos emplazados en mallas y capas internas donde se requiere tener un control preciso de su temperatura de trabajo. La clave, la precisión, el método y sobre todo, la repetición de cada ensayo en las mismas condiciones permite conseguir esa evaluación final en la que la marca convierte el prototipo ya en un neumático de producción o por el contrario, requiere intervención desde otras áreas para definir nuevas características. Medio siglo durante el cual Michelin ha mantenido absoluta confidencialidad y que por fortuna hemos tenido ocasión de conocer en vivo en una entretenida y didáctica jornada de trabajo.